Sourcing Grace Farms’ Roof
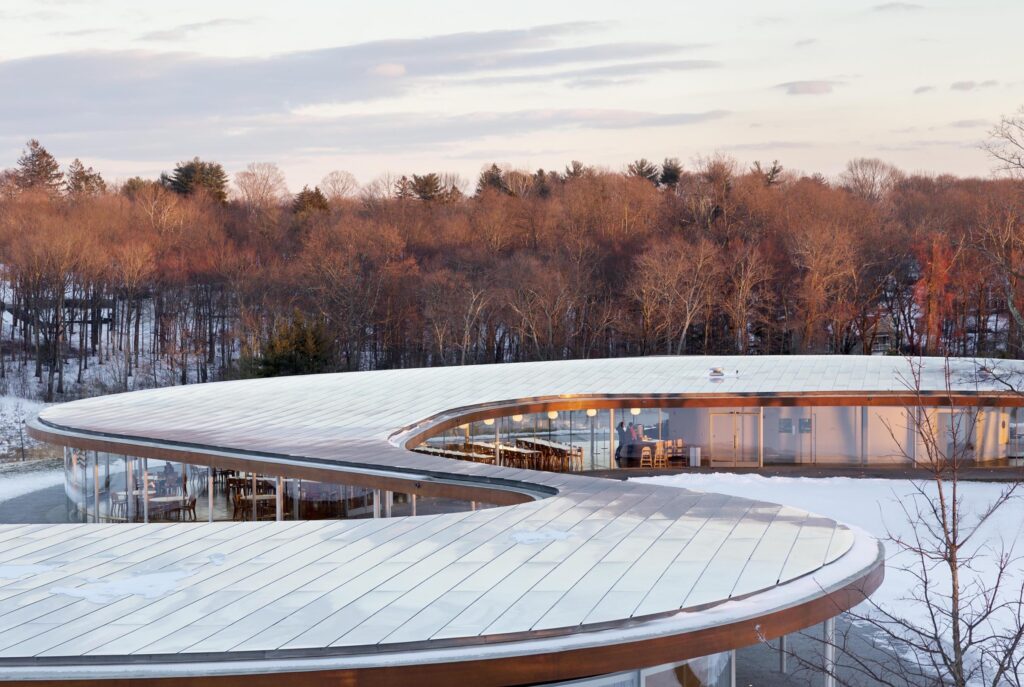
Introduction
In 2015, Grace Farms completed construction of its new center in New Canaan, Connecticut, designed by SANAA, an internationally recognized Pritzker Prize-winning firm. The project was met with enthusiastic reviews from the public and the design community for its seamless integration of nature, geometry, and materials. Those materials: glass, wood, metals, and concrete, are sourced from contractors, vendors, and suppliers that Sciame Construction, the general contractor, employed for the construction of the building.
As one of the founding members of Grace Farms’ Design for Freedom Working Group, in 2019 Sciame Construction was asked to take a deep dive into the supply chain of the materials used in the construction of Grace Farms. The roof of Grace Farms is a highly visible and unique rain-screen system that took years to design, engineer, and fabricate. The following pages describe the methods used to reveal the global supply chain of the roof and critical findings and shortfalls of this investigation.
Methodology
The 60,000 square-foot roof of Grace Farms is an aluminum rain-screen that covers the actual waterproofing system. A rain-screen is a decorative skin used to hide the roofing membrane but also provides additional protection from the elements and ultra-violet rays. Zahner Inc., a sheet metal manufacturer from Kansas City, Missouri, was hired by Sciame to assist the architects with realizing the roof system and fabricating it. After a one-year design process that involved many decisions on costs, finishes, and constructability studies, a fully realized design was achieved. The aluminum roof consists of several parts that include rails, gutters, clips, standoffs, panels, and mesh screens.
Exhibit A: Grace Farms Roof Suppliers
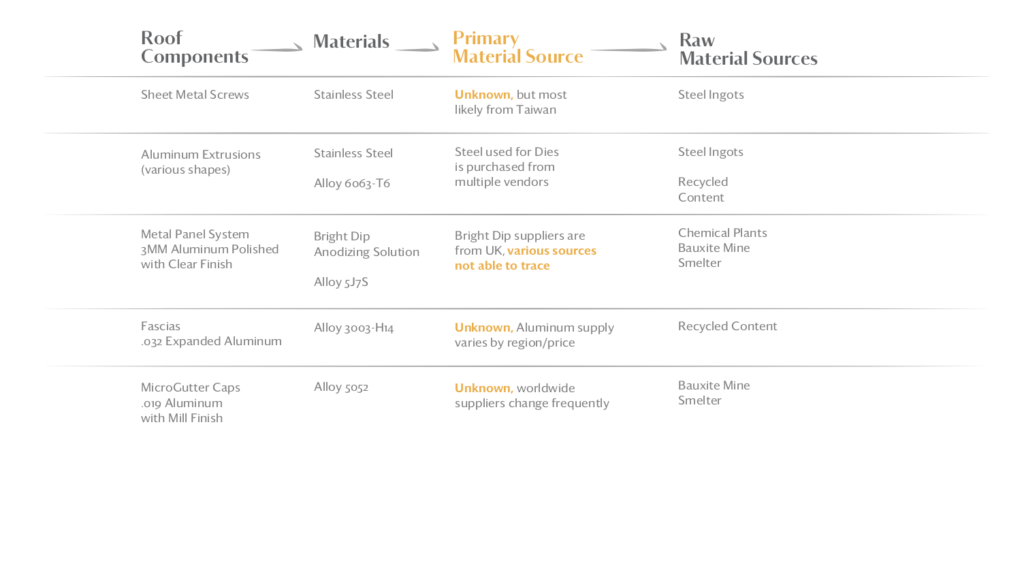
In 2019, Sciame started a forensic survey by first cataloging each material into a matrix that indicated the primary materials and secondary materials. Zahner then offered a list of suppliers that provided the raw or manufactured materials that they would, in turn, cut, shape, and bend into the rain-screen system. These suppliers are primarily located throughout the U.S., where forced labor is illegal.
After establishing the primary suppliers of the roof components to Zahner, Sciame contacted each company and inquired about how they purchased their materials. If those firms were able to, they provided Sciame with additional contacts or leads further down in the supply chain.
Sciame then contacted the purchasing departments for each of the suppliers. They, in turn, provided contacts for raw material suppliers or purchasing agents if the information was available.
The research conducted led to the development of the chart titled “Exhibit A.” The source of items in orange cannot be identified, due to two main reasons:
- First, the purchasing departments of the suppliers to Zahner did not keep records for the materials specific to their customer, Zahner. For example, Fastenal, the screw supplier, purchased stainless steel to maintain stock. That stock contained stainless steel from multiple sources. Therefore, no conclusion could be reached as to whether the screws used in the Grace Farms project were produced using forced labor or not.
- Second, some purchasing departments explained that they buy raw material every day from different commodity brokers who are always adjusting their prices based on global market conditions. The source of the raw material may not even be known to the broker, who is often dealing with a network of buyers and sellers worldwide. This was the case for the aluminum where it is made at smelting plants, located across Asia with raw and recycled materials. Again, this led to an indeterminate conclusion about the nature of the labor used to produce the raw material.
The purchasing departments who Sciame contacted did reference a chain of custody form that could be used for future purchases. This form would indicate the origins of each component and how they traveled from factory to factory. However, this process must be set up early in the lifespan of the project, and it requires oversight and management, potentially leading to additional project costs, which should be considered by the project stakeholders.
Conclusion
Tracing the origins of any material is a formidable task that requires some understanding of the manufactured goods and commodity markets. Often a builder, owner, or architect will specify a material or piece of equipment without considering the issue of who makes it. These decisions are typically made early in the design process and concern themselves with questions like aesthetics or budgets. However, asking how the supply chain operates should be measured alongside those considerations. For example, can we take an ethical approach to material selection and integrate it into the decision making process? And how does one verify that all parties along the supply chain are adhering to those values? Can technology help trace the lifespan of an air conditioner, a light fixture, or a concrete block? Can it help pinpoint the actual people who touched it and if those people are being paid equitably and treated fairly?
Key Takeaways
- Acknowledge that buildings, which consist of thousands of complex parts, have an opaque supply chain where questions of ethical labor practices cannot be fully understood.
- As a project stakeholder, commit early on in the design process to ask where each material might come from and revise your selections to avoid benefitting from unfair labor practices. Get buy-in from all other stakeholders on the project. Use contract language or incentives to compel suppliers and vendors
- Enact a system for tracking and monitoring where materials and equipment originated. Use technology to collect and analyze data. Verify the accuracy of the information with periodic checks and address grey areas.